The Latest from Southeast Farm Press
Cotton seedling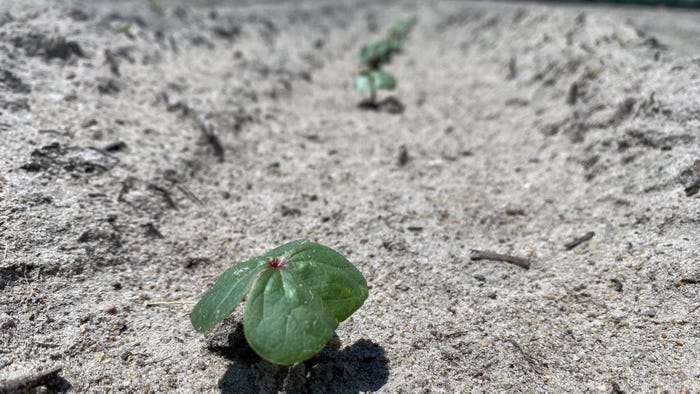
Cotton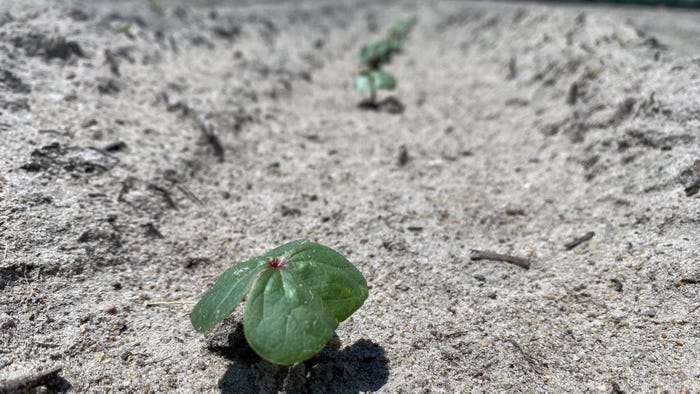
Thrips predictor hones cotton plansThrips predictor hones cotton plans
The N.C. State University Thrips Infestation Predictor is based on local weather forecasts, and accuracy improves closer to planting. Growers should check it just prior to planting.
Market Overview
Contract | Last | Change | High | Low | Open | Last Trade |
---|---|---|---|---|---|---|
Jul 24 Corn | 452.75 | +0.75 | 453 | 451.5 | 451.75 | 02:30 AM |
Jul 24 Oats | 356.5 | +5.5 | 356.5 | 352.25 | 352.25 | 02:28 AM |
May 24 Class III Milk | 18.28 | +0.1 | 18.28 | 18.28 | 18.28 | 10:00 PM |
Jul 24 Soybean | 1179.5 | -0.25 | 1181 | 1178 | 1179 | 02:30 AM |
Aug 24 Feeder Cattle | 258.3 | +2 | 258.8 | 254.25 | 256.425 | 06:04 PM |
May 24 Ethanol Futures | 2.161 | unch — | 2.161 | 2.161 | 2.161 | 09:38 PM |

Copyright © 2019. All market data is provided by Barchart Solutions.
Futures: at least 10 minute delayed. Information is provided ‘as is’ and solely for informational purposes, not for trading purposes or advice.
To see all exchange delays and terms of use, please see disclaimer.
All Southeast Farm Press
Subscribe to receive top agriculture news
Be informed daily with these free e-newsletters